Coal Gasifier is designed to be high production capacity, high gasification efficiency and better adaptability to various coals, high gas calorific value, and only need two worker to operate it, our coal gasifier can cope with different type heating furnace, kiln, steam boiler and ect.
Our company design and manufacture environmentally friendly coal gasifier that based on the air and steam as gasification agent and is the advanced equipment that produce mixed gas. The equipment is suitable for gasifying coking coal, coke and other fuels, are widely used as furnace kiln of machinery, metallurgy, chemical industry, glass, building materials, light industry, food, textile industry.
CO: 23-27%
H2: 12-17%
CH4: 2-3.5%
CO2: <5%
N2: 50-54%
As shown, the composition of the syngas can vary quite significantly, depending on the coal feedstock used, and the type of gasification reactor system and its operating conditions.
2) Easy to operate and maintain;
3) Long service life;
4) Continual and cyclical manufacturing;
5) It is safe to use for with double safe control;
6) Evenly combusting.
Application of Coal gas Gasifier, coal gasifier plant
Coal Gas Generator which designed and manufactured by our company use air and water vapor as the gasification agent, is the advanced equipment. It can product mixed-gas, fit gasify coke and other fuels. Coal gas generator is widely used in machinery, metallurgical, chemical, glass, building materials, light industry, food, textile industry.
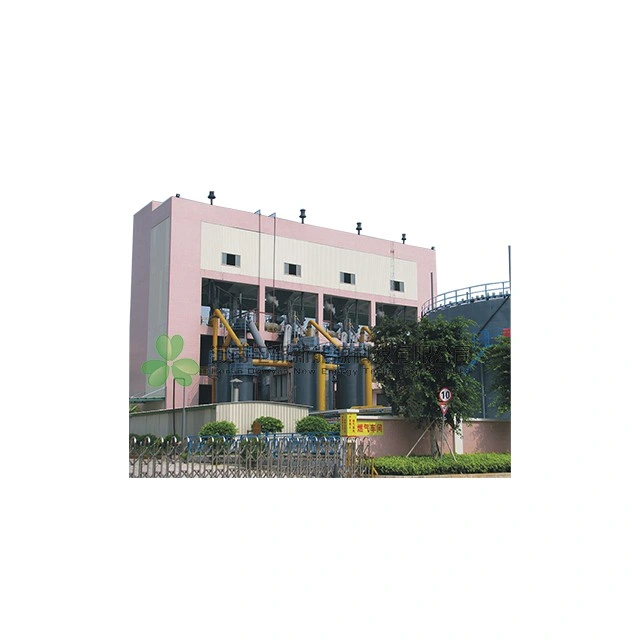
Product Parameters
Model | QM0.8 | QM1.0 | QM1.2 | QM1.5 | QM1.6 | QM1.8 | QM2.0 | QM2.4 | QM2.6 | QM3.0 | QM3.2 |
Chamber diameter(mm) | 800 | 1000 | 1200 | 1500 | 1600 | 1800 | 2000 | 2400 | 2600 | 3000 | 3200 |
Hearth active surface(m2) | 0.5 | 0.785 | 1.13 | 1.77 | 2.01 | 2.54 | 3.14 | 4.52 | 5.31 | 7.07 | 8.04 |
Suirable fuel | weak coherent gas carbon,anotherracite,burnt carbon | ||||||||||
Fuel granularity(mm) | 25-80 | ||||||||||
Fuel consumption quantitykg/h | 40-100 | 70-140 | 120-190 | 160-350 | 350-460 | 500-600 | 500-720 | 700-1040 | 850-1200 | 1700-2000 | 1800-2200 |
Gasifying agent | Air ,steam | ||||||||||
Gas yieldNm³/h) | 140-350 | 245-490 | 420-670 | 560-1200 | 1200-1600 | 1500-2100 | 1750-2500 | 2500-3600 | 3000-4300 | 6000-7000 | 6500-7500 |
Gas calorific valu(Kj/Nm³ | 5020-5670 | 5020-6000 | |||||||||
Water jacket heating area() | 4.02 | 5.02 | 6.78 | 10.37 | 11.06 | 12.44 | 17.58 | 21.87 | 23.69 | 30.16 | 32 |
Steam outputkg/h | 60 | 80 | 130 | 200 | 220 | 260 | 350 | 420 | 600 | 840 | 200 |
Gas outlet temperature() | (400-500)Plants related with the coal | (400-500)Plants related with the coal | |||||||||
Gas outlet pressure(Pa) | 1000 | 980-1470 | 1470-1960 | 980-1470 | |||||||
Gas exportation diameter(mm) | 219 | 325 | 325 | 426 | 426 | 529 | 630 | 720 | 820 | 1020 | 900 |
Air pressure(Pa) | 3000 | 4000 | 3000 | ||||||||
Saturated air temperature() | 50-60 | 50-65 | |||||||||
Ashpan rotational speed(r/h) | 0.177-1.77 | ||||||||||
Equipment gross weight(t) | 3.5 | 4.5 | 5 | 7.5 | 10 | 20 | 23.4 | 29.8 | 32 | 37.6 | 16 |
Process of the coal gasifier
During gasification, the coal is blown through with oxygen and steam (water vapor) while also being heated (and in some cases pressurized). If the coal is heated by external heat sources the process is called "allothermal", while "autothermal" process assumes heating of the coal via exothermal chemical reactions occurring inside the gasifier itself. It is essential that the oxidizer supplied is insufficient for complete oxidizing (combustion) of the fuel. During the reactions mentioned, oxygen and water molecules oxidize the coal and produce a gaseous mixture of carbon dioxide (CO2), carbon monoxide (CO), water vapour (H2O), and molecular hydrogen (H2). (Some by-products like tar, phenols, etc. are also possible end products, depending on the specific gasification technology utilized.) This process has been conducted in-situ within natural coal seams (referred to as underground coal gasification) and in coal refineries. The desired end product is usually syngas (i.e., a combination of H2 + CO), but the produced coal gas may also be further refined to produce additional quantities of H2:
If the refiner wants to produce alkanes (i.e., hydrocarbons present in natural gas, gasoline, and diesel fuel), the coal gas is collected at this state and routed to a Fischer-Tropsch reactor. If, however, hydrogen is the desired end-product, the coal gas (primarily the CO product) undergoes the water gas shift reaction where more hydrogen is produced by additional reaction with water vapor:
CO + H2O → CO2 + H2
Although other technologies for coal gasification currently exist, all employ, in general, the same chemical processes. For low-grade coals (i.e., "brown coals") which contain significant amounts of water, there are technologies in which no steam is required during the reaction, with coal (carbon) and oxygen being the only reactants. As well, some coal gasification technologies do not require high pressures. Some utilize pulverized coal as fuel while others work with relatively large fractions of coal. Gasification technologies also vary in the way the blowing is supplied
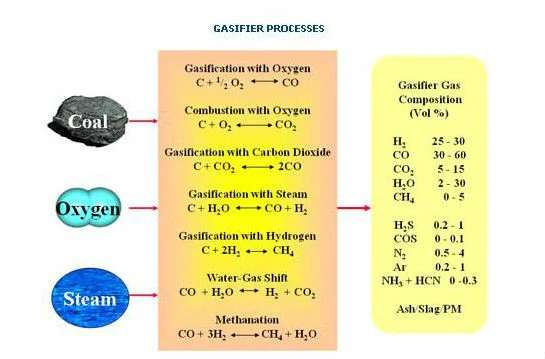
1.Are you a manufacturer or trading company?
We are a private machine manufacturer which have12 years experience in coal gas machine.
We have matural tech and reasonable price.
2.Any customers around your factory for checking?
We have many customers close to us.We warmly welcome you if you want to come.
Pre-sale services:
(1) device model choice.
(2) According to customer's special requirements, design and manufacture of products.
(3) Training technical personnel for clients.
(4) The company is free of charge to the user on-site engineering and technical personnel planning site for the user to design the best processes and program
After-sale services :
(1) free to assign a dedicated service personnel, arriving at the scene and guiding customers' installation.
(2) equipment installation.
(3) on-site training of operators.
(4) complete sets of equipment installed, 1-2 full-time technical staff to stay free of charge to help customers on-site production of 1 month, until the user' satisfaction